[DIY или Сделай сам] Переделка CNC 3018 Pro на рельсы. Личный опыт. Часть 1
Автор
Сообщение
news_bot ®
Стаж: 7 лет 6 месяцев
Сообщений: 27286
Дамы и господа, здравствуйте!Опишу тех. процесс доработки станочка. Так же предложу варианты (если это возможно) для упрощения доработки. Основной посыл данного поста - не бояться работать руками!Технология переделки не моя, акцентирую на этом внимание.При написании статьи я не "лазил" по инету, проверяя правильность своих мыслей.Все советы основаны исключительно на моём личном опыте, который вырабатывался годами.Если какой-то совет читателям покажется странным или вредным, прошу указать на это в комментариях.И последнее. В статье будут видеоролики, но исключительно тогда, когда я не смогу описать словами или фотками текущий процесс.Всё изложено тут: Переделка 3018 PRO на линейные рельсы. Введение и далее по ссылкам статьи.Если вы почитаете статьи из ссылки, то там в принципе всё понятно что и как, но не описан сам процесс переделки. Т.е. даны чертежи, в комментариях приводятся различные варианты доработок, а вот как это всё происходит, не описано. Оговорка 1.Станочек из "коробки" вполне работоспособен. Я его использую для изготовления прототипов печатных плат (сверловка и обрезка по контуру). Сверловка проходит нормально - делал ПП размерами порядка 150х100 с переходными отверстиями 0.3мм. (около ста переходных отверстий + "рабочие"). Шаблон ПП печатал на струйнике, и отверстия с шаблоном более-менее сходились (повторюсь, это прототипы). А вот обрезка по контуру мне очень не понравилась - жесткости не хватает (понятно, что можно играться с глубиной и со скоростью подачи, но хочется ведь быстрее :) ). В итоге, решил переделать станочек на рельсы, чтобы повысить жесткость.Кратко суть переделки.Все направляющие станочка, это валы. И, если ось Y, с натяжкой можно сказать "жесткая", то ось X это пластилин - слегка надавливая пальцем на каретку Z сверху, вижу невооруженным глазом смещение шпинделя вниз и в плоскости Y - назад. Так же (это именно на моём станке) была разность высот по оси Z при перемещении по оси X порядка 0.8мм., что ни в какие ворота (обходился щупом, строя карту высот) - и конечно же переходные отверстия печатных плат 0.3мм были овалом и не сходились с шаблоном.Итого.Все валы заменяются на рельсы MGN12, которые крепятся на профили 2040. Самое сложное это ось Z. Но пойдем по порядку (вначале ось Y, потом Х и в конце Z).Оговорка 2.У меня есть много инструментов и оснастки разного назначения, начиная от дрели и заканчивая станками: фрезерный и токарный (китайцы). Так же есть погружная пила ... хвалюсь хвалюсь, но для изготовления нестандартной мебели, самое то!. Покупалось всё постепенно, когда находились свободные денежные средства, которые не приносили "урон" семье.Опыт приходил с годами, начиная от... 80го года примерно. В то время я и мечтать не мог о, допустим электродрели, но при помощи ручной дрели, тисков, молотка, лобзика по дереву и т.д. изготовил механику кассетного магнитофона (блин, не могу найти, сфоткал бы :(( ). Т.е. у меня есть опыт, как при помощи "домашних" инструментов изготовить работающее изделие.Оговорка 3.Переделку можно сделать на "стороне" где есть ЧПУ станки, но конечно за деньгу (или по знакомству). Это неплохой вариант, и он явно будет качественнее, нежели делать в домашних условиях/в гараже. Каждый выбирает сам.Ладно, хватит соплей, перейду к сути.Как это всё делается ручками (лукавлю, извиняюсь).Вначале закупил все детали на Али по ссылкам из статьи, за исключением алюминиевых пластин для оси Z (их я покупал тут ) и крепежа (болты и шайбы). Просто доставка металла с Али очень дорогая, но как пишут в комментариях в статье по этому поводу, заготовки присылают хорошего качества (плоскость, кромки). Профили тоже можно было купить у нас, но чет я поторопился и заказал в Али. Кто живет в глубинке (а Казань я тоже считаю глубинкой, т.к., допустим профили здесь не купишь), советую заказать и крепеж. Для доработки станочка я буду использовать фрезерный станок JUM-X2 который у меня есть в наличии. Ухх сейчас закидают тряпками и будут негодовать по поводу "где в домашних условиях?". Отбиваясь от тряпок, я постараюсь дать несколько советов, как избежать использования станка (чую, в некоторых случаях это не получится :( )Ось Y.Почему изначально ось Y.Переделка оси X ну очень легкая. Нужно вместо валов добавить два профиля 2040, предварительно рассверлив два существующих отверстия и просверлив два дополнительных (см. статью) и … всё :) А вот дальше идет ось Z. Как я писал выше, она самая сложная в изготовлении. Поэтому решил попрактиковаться на "кошках", и в первую очередь переделать ось Y.Оговорка 4.При переделках работающей техники, я стараюсь продумать undo, т.е. возврат в исходное состояние (а вдруг позвонит работодатель и скажет "мне нужна тестовая плата"). В данной переделке это можно сделать, даже если вы решите переделывать в первую очередь ось X (профили можно повернуть на 90град. и поставить на место штатные оси).Итак, поехали.Оказывается есть разные вариации станочков cnc3018pro, в плане размеров. Напишу про которые прочитал на форуме:Ось Y, то бишь станина (ДхШ):1. 360х310 при толщине передней и задней планок 10мм. Т.е. длина профилей равна 290мм.2. 380х330 при толщине передней и задней планок 15мм. (вот тут могу ошибаться). Длина профиля при этом будет 300мм. (такая длина профиля была обозначена для покупки).Мой станочек варианта 1, т.е. мне нужен профиль длиной 290мм.Т.к. я закупил профиль 300мм., его нужно грамотно укоротить, в том плане, чтобы:1. По вертикали и горизонтали был угол 90град.2. Длина профиля должна быть как можно точнее.Укорачиваем профиль.Автор использовал торцовочную пилу - хороший вариант, но у меня её нет (думал о покупке, проделал мозговой штурм и решил, что она будет использоваться очень редко, не стал покупать).Как и советует автор статьи, не нужно делать отрез сразу "в размер". Лучше постепенно приближаться к исходному. Тут есть одно НО. По крайней мере у меня, штатные профили различались по длине (один был примерно на 0.5мм. длиннее другого). Поэтому, советую все четыре профиля сложить вместе и отрезать за несколько заходов, приближаясь к самому короткому профилю (короткий профиль тоже нужно чуток "захватить") - ну и что, что они все будут короче на, допустим 0.2мм. - в нашем случае это неважно (утрирую конечно).На станке профили я торцевал так: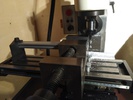
И так все четыре профиля, включая штатные.Фреза у меня 10мм. для ЧПУ станков (блин, острая, резался пару раз, когда вставлял в шпиндель).Слева упор, столик по оси X заблокирован. Длину торцевания выбирал по самому короткому профилю. Подводил полоску газетки между фрезой и профилем, и делал так, чтобы газетка рвалась (вращая фрезу при этом). Далее клинил столик (а при клине столик уходит порядка на 3 сотки). Делал проход по короткому профилю и затем делал другие.Кто в теме, наверное заметили, что тиски к столу станка я креплю не совсем правильно, но при таком крепеже, даже при работе со сталью, смещения не было (проверял). Естественно тиски были "прокатаны" индикатором ИРЦ (не, у меня точность не такая как на фотке ниже, у моего 0.01мм):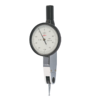
Уголок тут не поможет.Долго думал, как можно торцевать профиль без станка, или без торцовки... чет в голову пришли только такие мысли:- самое очевидное, это заказать обрезку там, где будете покупать профиль (но с малой долей вероятности могут ошибиться с размером);- или заказать сразу четыре профиля (взамен двух существующих) в размер;- фрезером по дереву, используя упор, например, профильную алюминиевую трубу или уголок, что как грязи во всех магазинах (блин за глубинку обидно...) - лично ровнял алюминий таким фрезером, потихоньку конечно;- дисковая пила? Но тут нужен стол... не знаю;- ножовка по шаблону? Вообще не вариант ИМХО;Короче, если нет станка/торцовки, я бы отдал на завод все четыре профиля, и пусть они отторцуют их. Да, тут я слился :(Профили укоротили, можно приступить или к нарезке резьбы в торцах новых профилей (резьбы то там нет :) ) или к разметке и сверловке передней и задней планок, к которым эти профили будут крепиться.Отдохнем :) Нарежем резьбу.Нарезка резьбы.В профиле у нас отверстие диаметром 5мм., что как раз соответствует диаметру отверстия под резьбу М6.Справка.Диаметр отверстия под резьбу считается так: резьба минус шаг резьбы. Т.е. у нас резьба М6 минус шаг резьбы (в данном случае стандартный, и он 1мм.) получается 5мм., что и имеем. Кстати, для алюминия я немного уменьшаю диаметр отверстия, т.к. алюминий материал пластичный и резьба будет жестче (зависит от диаметра резьбы). Для резьбы М6, я бы дал диаметр 4.8-4.9мм.По метчикам.У меня метчики с советских времен, они двух-трех проходные. Т.е. на резьбу используются два-три метчика, они помечены номерами, например, М6 1, М6 2 - цифры (1,2) пишут обычно ниже обозначения резьбы, т.к. числа рядом с резьбой, обозначают шаг. Пишу по памяти, поэтому поправьте, если ошибаюсь (просто на метчиках, которые я использовал, такой инфы не было). Вот метчики, которые я использовал для нарезки резьбы в профилях: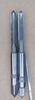
По фотке, метчик слева это первый номер, справа - второй. Видно, что левый метчик чуть длиннее и кончик более "вытянутый". Если на глаз не можете определить номер метчика, то возьмите гайку соответствующего диаметра и попробуйте навернуть её на метчик. Если гайка наворачивается легко, то это явно номер 1. Если наворачивается с трудом, то номер 2. Если же гайка вообще не наворачивается ни на один из метчиков, значит или у гайки шаг резьбы другой, или у метчика другой шаг. Или, гайка имеет левую резьбу, или метчик имеет левую резьбу (левая резьба вовсю используется в элементах вращения, например в креплении крыльчаток пылесосов).Сейчас вроде бы везде продают однопроходные метчики, т.е. совмещают номер 1 и номер 2.Шаг резьбы.Есть стандартные шаги резьб, а есть нестандартные (такие используются, например, в машинах и не только). В магазинах типа "Максидом", "Леруа" и т.д. вы явно не найдете метчики с нестандартным шагом, поэтому, если у вас нет метчика, смело покупайте их в "таких" магазинах (но сейчас это явно будет китай, но для алюминия пойдет).Всё, ликбез окончен.Приступаем к нарезке.Операция нехитрая, описание нарезки резьбы вы найдете во многих источниках. Единственное что скажу, везде будут писать, что метчик нужно начинать вворачивать строго под 90град и смазывать хитрым составом или жиром/маслом определенной марки и т.д. Насчет вворачивания под 90град.В нашем случае, если сильно не давить на метчик на начальном этапе, то он сам войдет в отверстие как надо. И далее, нужно легонько вворачивать его дальше, пока он не "захватится". Ну а дальше уже по инструкциям из инета. По поводу смазки: я использовал обычное машинное масло, незнай какой марки (можно вообще без масла, но будет туже идти).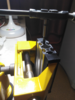
Кстати советую приобрести такие тиски. Они хоть и "пластилиновые", но для работ пойдут. Просто их крутить/вертеть как хошь можно.Глубина резьбы, чем больше, тем лучше. Я резал на всю длину метчиков - получилось порядка 20мм.После нарезки резьбы (у меня по крайней мере) остается бортик вокруг отверстия - я его прозенковал сверлом 10мм. руками.Разметка и сверловка передней и задней планки оси Y.Материал планок осей X,Y это полиацеталь. Он хорошо сверлится, т.е. его можно сверлить руками. Самое главное грамотно разметить :)Вот что нужно разметить/просверлить (на этом чертеже не показаны существующие отверстия под валы, они находятся чуть ближе к краям относительно новых отверстий):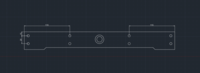
Вот они: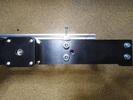
А левее/правее уже просверленные отверстия (профили я уже прикрепил).Чтобы не было несоосностей новых отверстий, я скрепил обе планки винтами - 6 винтов по всем существующим отверстиям в планках. Важно добиться совмещения плоскостей планок по какой-то базе (а планки нифига не одинаковые). Я совмещал планки по верхней плоскости и по одной из боковых - от этого совмещения я и "плясал" в плане разметки новых отверстий.Вот что получилось, зажав бутерброд:Извините, данный ресурс не поддреживается. :( Вначале видно, что уход на десятку, но я это списываю на неровность начала края. Далее, видите сами.Совет.Планки у нас прижимаются к столу станка прижимами, но между планкой и столом нужно оставить зазор, чтобы сверло не уперлось в стол в конце сверления. За счет скрепляющих болтов этот зазор так и так будет, но он не будет гарантированно одинаковым по всей длине планки, т.к. длины болтов или толщина их шляпок могут быть разными. В итоге планка, относительно стола станка, может оказаться под углом (небольшим конечно, и на глаз не увидишь) и отверстие будет овалом. Напрашиваются подкладки вида: гаек, кусочков фанеры и т.д., но они всё равно не будут гарантированно одинаковой высоты. Я использую для этих целей подшипники одного типоразмера - они то уж точно одинаковой высоты. Так же снизу, в местах будущих отверстий, советую наклеить скотч (малярный или прозрачный), чтобы при выходе сверла не было сколов. Я это забыл сделать и получил небольшие сколы по краям отверстий.При ручной сверловке всё легче - кладем планку на небольшую плашку из ДСП, и сверлим через кондуктор (сколов не должно быть, ну или наклеиваем скотч). И так каждое отверстие. Продолжу по работе со станком. Далее, при помощи краеискателя: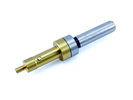
я нашел плоскости по X и Y.Краеискатель покупал на Али. Померил диаметр рабочей части - честные 4мм. (измерял "нашим" микрометром). Как им пользоваться, найдете в инете. Единственное - в некоторых видео проскакивало, что: "как только краеискатель не "бьет", значит край найден - неверно! Нужно, чтобы он сместился после того, как он отцентруется, вот тогда край найден. Насчет ошибки в позиционировании.... вроде бы, пишут порядка двух соток, читал на https://www.chipmaker.ru/ , но не помню где, там в разных топиках про это писали.Ну и далее по лимбам отмерил нужный размер и вначале сделал сверловку центровочным сверлом, а затем обычным.Если нет станка.Я бы разметил отверстия по штангенциркулю с глубиномером, примерно так: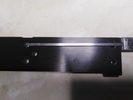
Тут два варианта:
- Делаем две риски чертилкой, или шариковой ручкой на скотче в верхней и нижней точке и затем проводим вертикаль;
- Делаем одну риску и затем, при помощи уголка, совмещая его по верхней базовой плоскости (вот только не пальчиками, а используя какую-либо плоскою пластину) например, алюминиевую прямоугольную трубу ( или что есть в наличии), проводим линию по уголку;Совмещение по уголку:
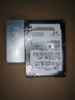
Извиняюсь, реальную пластину сфоткать не могу, поэтому вместо неё выступает HDD.Итого, в горизонтальной плоскости у нас две вертикальные линии (справа, слева).Далее, нужно от базы разметить по линиям центры двух отверстий. Делаем это глубиномером штангеля - вначале два отверстия по одному размеру, затем два - по другому.Суть в том, что, не меняя выставленный размер штангеля, мы размечаем отверстия на одинаковом расстоянии (плюс/минус конечно), и неважно, что мы ошибемся на ... допустим на 0.1-0.3 мм.. В горизонтали это вообще роли не играет, т.к. планки будут сверлиться вместе, а по вертикали... ну, конечно нужно как можно точнее.Шариковая ручка, почему?Разметку я всегда делаю шариковой ручкой (по малярному скотчу) с тонким пишущим узлом. Всегда так делаю, при изготовлении мебели для себя (т.к., карандаш всегда будет "врать" после каждого прохода по линейке - истирается).Центры отверстий размечены, далее сверловка. Шилом намечаю будущие отверстия (т.к. материал у нас не сталь) и затем шуроповертом со сверлом, диаметром порядка 2мм. делаю лунку. И теперь засада :) Нужно просверлить отверстия шуроповертом/дрелью в двух совмещенных планках перпендикулярно. Ручками не выйдет - отверстия будут овальными (или есть рукастые ? ). Я использую такой кондуктор: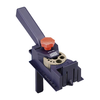
Явно есть другие кондукторы.В итоге получаем перпендикулярные отверстия.Всё, с передними/задними планками закончили, скрепляем их профилями. Получилось так: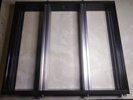
Далее изготовление пластин, скрепляющие каретки рельс со столиком, но это уже будет в следующей статье, если конечно читатели своими плюсами/минусами и комментариями, выскажут свои мнения по первой части.Спасибо!
===========
Источник:
habr.com
===========
Похожие новости:
- [DIY или Сделай сам] Математика, красота, любовь — история одной валентинки
- [Разработка под Arduino, DIY или Сделай сам, Электроника для начинающих] Сброс пробега для RICOH SP 150SUw
- [Rust, Производство и разработка электроники, DIY или Сделай сам] Фитнес-трекер для скейта
- [Программирование, Assembler, Научно-популярное, Старое железо, DIY или Сделай сам] Пишем программу для компьютера ALTAIR 8800 1975г выпуска
- [FPGA, Прототипирование, Схемотехника, Производство и разработка электроники, DIY или Сделай сам] Реализация процессорной архитектуры из книги Чарльза Петцольда «Код. Тайный язык информатики»
- [AR и VR, Нанотехнологии, Физика, DIY или Сделай сам, Лазеры] Как мы новую технологию AR очков придумывали (hardware)
- [Open source, DIY или Сделай сам, Микросервисы, Kubernetes] Новая версия нашего самописного плагина, который скачали 250 тысяч раз
- [Беспроводные технологии, DIY или Сделай сам, Звук] И снова CSR8645, или «надоело чинить провода»
- [JavaScript, Программирование, HTML, Браузеры, DIY или Сделай сам] How I create browser applications inside browsers (перевод)
- [Дизайн, DIY или Сделай сам, Урбанизм, Удалённая работа] Рабочее место на 0,5 м2
Теги для поиска: #_diy_ili_sdelaj_sam (DIY или Сделай сам), #_cnc3018, #_cnc, #_chpu (чпу), #_diy_ili_sdelaj_sam (
DIY или Сделай сам
)
Вы не можете начинать темы
Вы не можете отвечать на сообщения
Вы не можете редактировать свои сообщения
Вы не можете удалять свои сообщения
Вы не можете голосовать в опросах
Вы не можете прикреплять файлы к сообщениям
Вы не можете скачивать файлы
Текущее время: 26-Авг 01:16
Часовой пояс: UTC + 5
Автор | Сообщение |
---|---|
news_bot ®
Стаж: 7 лет 6 месяцев |
|
Дамы и господа, здравствуйте!Опишу тех. процесс доработки станочка. Так же предложу варианты (если это возможно) для упрощения доработки. Основной посыл данного поста - не бояться работать руками!Технология переделки не моя, акцентирую на этом внимание.При написании статьи я не "лазил" по инету, проверяя правильность своих мыслей.Все советы основаны исключительно на моём личном опыте, который вырабатывался годами.Если какой-то совет читателям покажется странным или вредным, прошу указать на это в комментариях.И последнее. В статье будут видеоролики, но исключительно тогда, когда я не смогу описать словами или фотками текущий процесс.Всё изложено тут: Переделка 3018 PRO на линейные рельсы. Введение и далее по ссылкам статьи.Если вы почитаете статьи из ссылки, то там в принципе всё понятно что и как, но не описан сам процесс переделки. Т.е. даны чертежи, в комментариях приводятся различные варианты доработок, а вот как это всё происходит, не описано. Оговорка 1.Станочек из "коробки" вполне работоспособен. Я его использую для изготовления прототипов печатных плат (сверловка и обрезка по контуру). Сверловка проходит нормально - делал ПП размерами порядка 150х100 с переходными отверстиями 0.3мм. (около ста переходных отверстий + "рабочие"). Шаблон ПП печатал на струйнике, и отверстия с шаблоном более-менее сходились (повторюсь, это прототипы). А вот обрезка по контуру мне очень не понравилась - жесткости не хватает (понятно, что можно играться с глубиной и со скоростью подачи, но хочется ведь быстрее :) ). В итоге, решил переделать станочек на рельсы, чтобы повысить жесткость.Кратко суть переделки.Все направляющие станочка, это валы. И, если ось Y, с натяжкой можно сказать "жесткая", то ось X это пластилин - слегка надавливая пальцем на каретку Z сверху, вижу невооруженным глазом смещение шпинделя вниз и в плоскости Y - назад. Так же (это именно на моём станке) была разность высот по оси Z при перемещении по оси X порядка 0.8мм., что ни в какие ворота (обходился щупом, строя карту высот) - и конечно же переходные отверстия печатных плат 0.3мм были овалом и не сходились с шаблоном.Итого.Все валы заменяются на рельсы MGN12, которые крепятся на профили 2040. Самое сложное это ось Z. Но пойдем по порядку (вначале ось Y, потом Х и в конце Z).Оговорка 2.У меня есть много инструментов и оснастки разного назначения, начиная от дрели и заканчивая станками: фрезерный и токарный (китайцы). Так же есть погружная пила ... хвалюсь хвалюсь, но для изготовления нестандартной мебели, самое то!. Покупалось всё постепенно, когда находились свободные денежные средства, которые не приносили "урон" семье.Опыт приходил с годами, начиная от... 80го года примерно. В то время я и мечтать не мог о, допустим электродрели, но при помощи ручной дрели, тисков, молотка, лобзика по дереву и т.д. изготовил механику кассетного магнитофона (блин, не могу найти, сфоткал бы :(( ). Т.е. у меня есть опыт, как при помощи "домашних" инструментов изготовить работающее изделие.Оговорка 3.Переделку можно сделать на "стороне" где есть ЧПУ станки, но конечно за деньгу (или по знакомству). Это неплохой вариант, и он явно будет качественнее, нежели делать в домашних условиях/в гараже. Каждый выбирает сам.Ладно, хватит соплей, перейду к сути.Как это всё делается ручками (лукавлю, извиняюсь).Вначале закупил все детали на Али по ссылкам из статьи, за исключением алюминиевых пластин для оси Z (их я покупал тут ) и крепежа (болты и шайбы). Просто доставка металла с Али очень дорогая, но как пишут в комментариях в статье по этому поводу, заготовки присылают хорошего качества (плоскость, кромки). Профили тоже можно было купить у нас, но чет я поторопился и заказал в Али. Кто живет в глубинке (а Казань я тоже считаю глубинкой, т.к., допустим профили здесь не купишь), советую заказать и крепеж. Для доработки станочка я буду использовать фрезерный станок JUM-X2 который у меня есть в наличии. Ухх сейчас закидают тряпками и будут негодовать по поводу "где в домашних условиях?". Отбиваясь от тряпок, я постараюсь дать несколько советов, как избежать использования станка (чую, в некоторых случаях это не получится :( )Ось Y.Почему изначально ось Y.Переделка оси X ну очень легкая. Нужно вместо валов добавить два профиля 2040, предварительно рассверлив два существующих отверстия и просверлив два дополнительных (см. статью) и … всё :) А вот дальше идет ось Z. Как я писал выше, она самая сложная в изготовлении. Поэтому решил попрактиковаться на "кошках", и в первую очередь переделать ось Y.Оговорка 4.При переделках работающей техники, я стараюсь продумать undo, т.е. возврат в исходное состояние (а вдруг позвонит работодатель и скажет "мне нужна тестовая плата"). В данной переделке это можно сделать, даже если вы решите переделывать в первую очередь ось X (профили можно повернуть на 90град. и поставить на место штатные оси).Итак, поехали.Оказывается есть разные вариации станочков cnc3018pro, в плане размеров. Напишу про которые прочитал на форуме:Ось Y, то бишь станина (ДхШ):1. 360х310 при толщине передней и задней планок 10мм. Т.е. длина профилей равна 290мм.2. 380х330 при толщине передней и задней планок 15мм. (вот тут могу ошибаться). Длина профиля при этом будет 300мм. (такая длина профиля была обозначена для покупки).Мой станочек варианта 1, т.е. мне нужен профиль длиной 290мм.Т.к. я закупил профиль 300мм., его нужно грамотно укоротить, в том плане, чтобы:1. По вертикали и горизонтали был угол 90град.2. Длина профиля должна быть как можно точнее.Укорачиваем профиль.Автор использовал торцовочную пилу - хороший вариант, но у меня её нет (думал о покупке, проделал мозговой штурм и решил, что она будет использоваться очень редко, не стал покупать).Как и советует автор статьи, не нужно делать отрез сразу "в размер". Лучше постепенно приближаться к исходному. Тут есть одно НО. По крайней мере у меня, штатные профили различались по длине (один был примерно на 0.5мм. длиннее другого). Поэтому, советую все четыре профиля сложить вместе и отрезать за несколько заходов, приближаясь к самому короткому профилю (короткий профиль тоже нужно чуток "захватить") - ну и что, что они все будут короче на, допустим 0.2мм. - в нашем случае это неважно (утрирую конечно).На станке профили я торцевал так: ![]() И так все четыре профиля, включая штатные.Фреза у меня 10мм. для ЧПУ станков (блин, острая, резался пару раз, когда вставлял в шпиндель).Слева упор, столик по оси X заблокирован. Длину торцевания выбирал по самому короткому профилю. Подводил полоску газетки между фрезой и профилем, и делал так, чтобы газетка рвалась (вращая фрезу при этом). Далее клинил столик (а при клине столик уходит порядка на 3 сотки). Делал проход по короткому профилю и затем делал другие.Кто в теме, наверное заметили, что тиски к столу станка я креплю не совсем правильно, но при таком крепеже, даже при работе со сталью, смещения не было (проверял). Естественно тиски были "прокатаны" индикатором ИРЦ (не, у меня точность не такая как на фотке ниже, у моего 0.01мм): ![]() Уголок тут не поможет.Долго думал, как можно торцевать профиль без станка, или без торцовки... чет в голову пришли только такие мысли:- самое очевидное, это заказать обрезку там, где будете покупать профиль (но с малой долей вероятности могут ошибиться с размером);- или заказать сразу четыре профиля (взамен двух существующих) в размер;- фрезером по дереву, используя упор, например, профильную алюминиевую трубу или уголок, что как грязи во всех магазинах (блин за глубинку обидно...) - лично ровнял алюминий таким фрезером, потихоньку конечно;- дисковая пила? Но тут нужен стол... не знаю;- ножовка по шаблону? Вообще не вариант ИМХО;Короче, если нет станка/торцовки, я бы отдал на завод все четыре профиля, и пусть они отторцуют их. Да, тут я слился :(Профили укоротили, можно приступить или к нарезке резьбы в торцах новых профилей (резьбы то там нет :) ) или к разметке и сверловке передней и задней планок, к которым эти профили будут крепиться.Отдохнем :) Нарежем резьбу.Нарезка резьбы.В профиле у нас отверстие диаметром 5мм., что как раз соответствует диаметру отверстия под резьбу М6.Справка.Диаметр отверстия под резьбу считается так: резьба минус шаг резьбы. Т.е. у нас резьба М6 минус шаг резьбы (в данном случае стандартный, и он 1мм.) получается 5мм., что и имеем. Кстати, для алюминия я немного уменьшаю диаметр отверстия, т.к. алюминий материал пластичный и резьба будет жестче (зависит от диаметра резьбы). Для резьбы М6, я бы дал диаметр 4.8-4.9мм.По метчикам.У меня метчики с советских времен, они двух-трех проходные. Т.е. на резьбу используются два-три метчика, они помечены номерами, например, М6 1, М6 2 - цифры (1,2) пишут обычно ниже обозначения резьбы, т.к. числа рядом с резьбой, обозначают шаг. Пишу по памяти, поэтому поправьте, если ошибаюсь (просто на метчиках, которые я использовал, такой инфы не было). Вот метчики, которые я использовал для нарезки резьбы в профилях: ![]() По фотке, метчик слева это первый номер, справа - второй. Видно, что левый метчик чуть длиннее и кончик более "вытянутый". Если на глаз не можете определить номер метчика, то возьмите гайку соответствующего диаметра и попробуйте навернуть её на метчик. Если гайка наворачивается легко, то это явно номер 1. Если наворачивается с трудом, то номер 2. Если же гайка вообще не наворачивается ни на один из метчиков, значит или у гайки шаг резьбы другой, или у метчика другой шаг. Или, гайка имеет левую резьбу, или метчик имеет левую резьбу (левая резьба вовсю используется в элементах вращения, например в креплении крыльчаток пылесосов).Сейчас вроде бы везде продают однопроходные метчики, т.е. совмещают номер 1 и номер 2.Шаг резьбы.Есть стандартные шаги резьб, а есть нестандартные (такие используются, например, в машинах и не только). В магазинах типа "Максидом", "Леруа" и т.д. вы явно не найдете метчики с нестандартным шагом, поэтому, если у вас нет метчика, смело покупайте их в "таких" магазинах (но сейчас это явно будет китай, но для алюминия пойдет).Всё, ликбез окончен.Приступаем к нарезке.Операция нехитрая, описание нарезки резьбы вы найдете во многих источниках. Единственное что скажу, везде будут писать, что метчик нужно начинать вворачивать строго под 90град и смазывать хитрым составом или жиром/маслом определенной марки и т.д. Насчет вворачивания под 90град.В нашем случае, если сильно не давить на метчик на начальном этапе, то он сам войдет в отверстие как надо. И далее, нужно легонько вворачивать его дальше, пока он не "захватится". Ну а дальше уже по инструкциям из инета. По поводу смазки: я использовал обычное машинное масло, незнай какой марки (можно вообще без масла, но будет туже идти). ![]() Кстати советую приобрести такие тиски. Они хоть и "пластилиновые", но для работ пойдут. Просто их крутить/вертеть как хошь можно.Глубина резьбы, чем больше, тем лучше. Я резал на всю длину метчиков - получилось порядка 20мм.После нарезки резьбы (у меня по крайней мере) остается бортик вокруг отверстия - я его прозенковал сверлом 10мм. руками.Разметка и сверловка передней и задней планки оси Y.Материал планок осей X,Y это полиацеталь. Он хорошо сверлится, т.е. его можно сверлить руками. Самое главное грамотно разметить :)Вот что нужно разметить/просверлить (на этом чертеже не показаны существующие отверстия под валы, они находятся чуть ближе к краям относительно новых отверстий): ![]() Вот они: ![]() А левее/правее уже просверленные отверстия (профили я уже прикрепил).Чтобы не было несоосностей новых отверстий, я скрепил обе планки винтами - 6 винтов по всем существующим отверстиям в планках. Важно добиться совмещения плоскостей планок по какой-то базе (а планки нифига не одинаковые). Я совмещал планки по верхней плоскости и по одной из боковых - от этого совмещения я и "плясал" в плане разметки новых отверстий.Вот что получилось, зажав бутерброд:Извините, данный ресурс не поддреживается. :( Вначале видно, что уход на десятку, но я это списываю на неровность начала края. Далее, видите сами.Совет.Планки у нас прижимаются к столу станка прижимами, но между планкой и столом нужно оставить зазор, чтобы сверло не уперлось в стол в конце сверления. За счет скрепляющих болтов этот зазор так и так будет, но он не будет гарантированно одинаковым по всей длине планки, т.к. длины болтов или толщина их шляпок могут быть разными. В итоге планка, относительно стола станка, может оказаться под углом (небольшим конечно, и на глаз не увидишь) и отверстие будет овалом. Напрашиваются подкладки вида: гаек, кусочков фанеры и т.д., но они всё равно не будут гарантированно одинаковой высоты. Я использую для этих целей подшипники одного типоразмера - они то уж точно одинаковой высоты. Так же снизу, в местах будущих отверстий, советую наклеить скотч (малярный или прозрачный), чтобы при выходе сверла не было сколов. Я это забыл сделать и получил небольшие сколы по краям отверстий.При ручной сверловке всё легче - кладем планку на небольшую плашку из ДСП, и сверлим через кондуктор (сколов не должно быть, ну или наклеиваем скотч). И так каждое отверстие. Продолжу по работе со станком. Далее, при помощи краеискателя: ![]() я нашел плоскости по X и Y.Краеискатель покупал на Али. Померил диаметр рабочей части - честные 4мм. (измерял "нашим" микрометром). Как им пользоваться, найдете в инете. Единственное - в некоторых видео проскакивало, что: "как только краеискатель не "бьет", значит край найден - неверно! Нужно, чтобы он сместился после того, как он отцентруется, вот тогда край найден. Насчет ошибки в позиционировании.... вроде бы, пишут порядка двух соток, читал на https://www.chipmaker.ru/ , но не помню где, там в разных топиках про это писали.Ну и далее по лимбам отмерил нужный размер и вначале сделал сверловку центровочным сверлом, а затем обычным.Если нет станка.Я бы разметил отверстия по штангенциркулю с глубиномером, примерно так: ![]() Тут два варианта:
![]() Извиняюсь, реальную пластину сфоткать не могу, поэтому вместо неё выступает HDD.Итого, в горизонтальной плоскости у нас две вертикальные линии (справа, слева).Далее, нужно от базы разметить по линиям центры двух отверстий. Делаем это глубиномером штангеля - вначале два отверстия по одному размеру, затем два - по другому.Суть в том, что, не меняя выставленный размер штангеля, мы размечаем отверстия на одинаковом расстоянии (плюс/минус конечно), и неважно, что мы ошибемся на ... допустим на 0.1-0.3 мм.. В горизонтали это вообще роли не играет, т.к. планки будут сверлиться вместе, а по вертикали... ну, конечно нужно как можно точнее.Шариковая ручка, почему?Разметку я всегда делаю шариковой ручкой (по малярному скотчу) с тонким пишущим узлом. Всегда так делаю, при изготовлении мебели для себя (т.к., карандаш всегда будет "врать" после каждого прохода по линейке - истирается).Центры отверстий размечены, далее сверловка. Шилом намечаю будущие отверстия (т.к. материал у нас не сталь) и затем шуроповертом со сверлом, диаметром порядка 2мм. делаю лунку. И теперь засада :) Нужно просверлить отверстия шуроповертом/дрелью в двух совмещенных планках перпендикулярно. Ручками не выйдет - отверстия будут овальными (или есть рукастые ? ). Я использую такой кондуктор: ![]() Явно есть другие кондукторы.В итоге получаем перпендикулярные отверстия.Всё, с передними/задними планками закончили, скрепляем их профилями. Получилось так: ![]() Далее изготовление пластин, скрепляющие каретки рельс со столиком, но это уже будет в следующей статье, если конечно читатели своими плюсами/минусами и комментариями, выскажут свои мнения по первой части.Спасибо! =========== Источник: habr.com =========== Похожие новости:
DIY или Сделай сам ) |
|
Вы не можете начинать темы
Вы не можете отвечать на сообщения
Вы не можете редактировать свои сообщения
Вы не можете удалять свои сообщения
Вы не можете голосовать в опросах
Вы не можете прикреплять файлы к сообщениям
Вы не можете скачивать файлы
Вы не можете отвечать на сообщения
Вы не можете редактировать свои сообщения
Вы не можете удалять свои сообщения
Вы не можете голосовать в опросах
Вы не можете прикреплять файлы к сообщениям
Вы не можете скачивать файлы
Текущее время: 26-Авг 01:16
Часовой пояс: UTC + 5