[CAD/CAM, DIY или Сделай сам] Гриндер: Ленточно-шлифовальный станок
Автор
Сообщение
news_bot ®
Стаж: 7 лет 6 месяцев
Сообщений: 27286
В последнее время в сети Интернет появилось достаточно много самодельных конструкций ленточно-шлифовальных станков, называемых в простонародье «гриндер». Вот и я решил не отклоняться от тенденции и сделать себе в мастерскую подобный станок. После изготовления этого станка он превзошел все мои ожидания.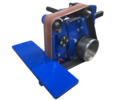
Про превзошедшие ожидания, конечно, громко сказано, но получившийся станок действительно показал хорошие результаты, хоть и сравнить особо было не с чем, разве что с теми, которые самоделки показывали на YouTube.Сам по себе станок довольно универсальный и может обрабатывать различные материалы (дерево, пластик, металл) с очень хорошей скоростью и поверхностной чистотой. В основе станка лежит шлифовальная лента, в моем случае она имеет размеры 50х900-1300 мм. Лента приводится в движение через шкив диаметром 128мм, установленный на вал асинхронного двигателя мощностью 1,1 кВт и максимальной частотой вращения 2980 об/мин. Исходя из этих данных можно рассчитать максимальную линейную скорость движения ленты, которая составит 1200 м/мин. Она ограничивается при помощи частотного преобразователя, подключенного к двигателю.Конструкция.Конструкция станка довольно простая, и при этом очень жесткая за счет своей массивности, так как в ее основу заложен лист толщиной 12 мм. Из него выполнено основание под асинхронный двигатель, к фланцу которого в свою очередь прикручена плита, образующая несущую раму всего станка. Чтобы хоть немного разгрузить фланец электродвигателя, основание и несущая рама связаны друг с другом через деталь - направляющую штанги. Далее в нее вставляется сама штанга, на один из концов которой крепится пластина, несущая на себе деталь в виде «полумесяца», а также направляющую для механизма установки рабочего столика. На концах «полумесяца» имеются два ролика, а через центр проходит ось, позволяющая поворачивать эту сборочную единицу под разными углами. Еще в состав сборочной единицы – «полумесяца», входит направляющий упор для шлифовальной ленты.На несущей раме через ось закреплен рычаг с роликом для центрирования шлифовальной ленты. Этот рычаг так же играет роль натяжителя, в виду того, что между ним и рамой установлен газлифт.Рабочие поверхности ведущего шкива и натяжного ролика имеют полукруглый усеченный профиль для лучшего удержания ленты на их поверхности.Механизм крепления рабочего столика имеет несколько степеней свободы, это делает его позиционирование очень удобным для последующей работы.
Изготовление и сборкаПроектирование этого станка продолжалось довольно долгое время. Все как я люблю – смоделировал в CAD программе, и раскидал деталировку с чертежами. Механической обработки получилось много, ее отдал другу – он занимается металлообработкой. Кроме токарных и фрезерных работ, требовалось изготовить еще ряд деталей из листового железа. Как вы уже, наверное, догадались, эти детали заказал на лазерной резке. В итоге, через некоторое время у меня в мастерской появился увесистый ящик с железом. И тут я смекнул: - «Если толком ничего не заработает, то при нынешних ценах на металл, сдам все в чермет и выйду в нули» (шутка конечно). Некоторые детали дорабатывал сам: сверлил отверстия, нарезал резьбы, сваривал, даже немного фрезеровал на своем СФ – 16 (но это отдельная история, так как опыта и знаний маловато). В общем, всю слесарную работу делал сам. Двигатель был куплен заранее.Началась сборка. Так как все было сделано по чертежам, то в целом собиралось хорошо - кайфанул. Но и без проблемных мест не обошлось, я все же человек, а людям, как известно, свойственно ошибаться. В паре деталях ошибся с размерами, в моделях, конечно, сразу все поправил, а вот с железом пришлось немного потрудиться, но и с ним все решилось.После предварительной сборки и пробного пуска, последовала разборка и покраска. Красить сам не стал, отдал «специалистам», все детали были отпескоструены и разделены на те, которые надо покрасить и на те, которые надо покрыть хим. оксидом. Покрасил уже традиционно в синий глянец, полимерной порошковой краской.Извините, данный ресурс не поддреживается. :( Работа и настройкаТак как у меня имелся частотный преобразователь на 1,5 кВт, то настройка упростилась. Вся настройка сводится к тому, чтобы при раскручивании ленты она не слетала с роликов и находилась всегда в одном и том же положении при прикладывании к ленте обрабатываемой детали.Для того чтобы ленту отцентровать, запустил вращение на малых оборотах и установочным винтом отрегулировал положение натяжного ролика. Далее постепенно увеличивал скорость вращения, чтобы убедиться, что лента отцентрована во всем диапазоне скоростей.Приступил к испытаниям. После прикладывания обрабатываемой детали к ленте, она начала смещаться в сторону. Отрегулировал положение направляющего упора между двумя роликами, расположенными на детали в виде «полумесяца». Ролики и направляющий упор должны находиться в одной плоскости, для этого даже пришлось отфрезеровать упор в угол, так как после сварки его немного повело.На этом основная настройка закончена, и можно приступать к работе. Тут многое зависит от обрабатываемого материала и требуемой шероховатости, которую необходимо получить, а, следовательно, для этого надо подбирать зернистость ленты и скорость ее вращения.Работать на этом станке еще только предстоит учиться, но уже кое-какой опыт получен.Извините, данный ресурс не поддреживается. :( Выводы и рекомендацииВ ходе эксплуатации также обнаружился пока один, но довольно весомый недостаток конструкции: не хватает мощности. Решения два: поставить мотор мощнее или уменьшить диаметр ведущего шкива. Второй вариант пока более предпочтителен, но с диаметром еще не определился.Возможно, в будущем переделаю немного основание для того чтобы была возможность поворачивать рабочую часть в горизонтальное положение. А в остальном пока все устраивает. Вариантов доработки конечно много, это и магнитный столик на каретке для шлифовки плоскости и всевозможные приспособы для удержания заготовок, установка дополнительных роликов и колёс различного диаметра и т.д. Вопрос ценыГриндер получился не из бюджетной категории. Подобного по качеству изготовления из того, что продается в Интернет-магазинах, я не видел. Местами можно конструкцию немного облегчить и тем самым удешевить, но не вижу особого смысла, так как станок изначально делался для себя. То, что продается в основном слеплено из листа заниженной толщины, нарезанного чпу лазером, все рассчитано на низкую себестоимость. Но самое главное то, что все они работоспособные и не важно, сколько металла в них заложено.
===========
Источник:
habr.com
===========
Похожие новости:
- [FPGA, Процессоры, DIY или Сделай сам, Электроника для начинающих] Zynq 7000. Собираем Linux для платы QMtech
- Выпуск Ultimaker Cura 4.10, пакета для подготовки модели к 3D-печати
- [Анализ и проектирование систем, Графические оболочки, Работа с 3D-графикой, CAD/CAM] Dassault Systèmes — новые горизонты строительной отрасли
- [Производство и разработка электроники] Как мы запускали собственную систему управления биореакторами BioGain
- [Разработка для интернета вещей, Интернет вещей, DIY или Сделай сам, Электроника для начинающих] Дружимся с ESP
- [Работа с 3D-графикой, Софт, Удалённая работа] Архитектурный бизнес в период удаленки: практика командной работы в Archicad
- [Open source, DIY или Сделай сам, Сотовая связь] Базовая станция LTE своими руками: такое возможно?
- [.NET, API, Google API, C#, DIY или Сделай сам] How to be good in hackathons as a developer? Practice creating simple pet projects
- [Читальный зал, Старое железо, DIY или Сделай сам] Превращение классического ЭЛТ в Smart TV (перевод)
- [Разработка под Arduino, DIY или Сделай сам] Управление прожекторами при помощи Arduino
Теги для поиска: #_cad/cam, #_diy_ili_sdelaj_sam (DIY или Сделай сам), #_grinder (Гриндер), #_diy, #_diy_ili_sdelaj_sam (diy или сделай сам), #_cad, #_kompas (компас), #_stanok (станок), #_shlifovalnyj_stanok (шлифовальный станок), #_shlifovanie (шлифование), #_cad/cam, #_diy_ili_sdelaj_sam (
DIY или Сделай сам
)
Вы не можете начинать темы
Вы не можете отвечать на сообщения
Вы не можете редактировать свои сообщения
Вы не можете удалять свои сообщения
Вы не можете голосовать в опросах
Вы не можете прикреплять файлы к сообщениям
Вы не можете скачивать файлы
Текущее время: 26-Авг 03:33
Часовой пояс: UTC + 5
Автор | Сообщение |
---|---|
news_bot ®
Стаж: 7 лет 6 месяцев |
|
В последнее время в сети Интернет появилось достаточно много самодельных конструкций ленточно-шлифовальных станков, называемых в простонародье «гриндер». Вот и я решил не отклоняться от тенденции и сделать себе в мастерскую подобный станок. После изготовления этого станка он превзошел все мои ожидания. ![]() Про превзошедшие ожидания, конечно, громко сказано, но получившийся станок действительно показал хорошие результаты, хоть и сравнить особо было не с чем, разве что с теми, которые самоделки показывали на YouTube.Сам по себе станок довольно универсальный и может обрабатывать различные материалы (дерево, пластик, металл) с очень хорошей скоростью и поверхностной чистотой. В основе станка лежит шлифовальная лента, в моем случае она имеет размеры 50х900-1300 мм. Лента приводится в движение через шкив диаметром 128мм, установленный на вал асинхронного двигателя мощностью 1,1 кВт и максимальной частотой вращения 2980 об/мин. Исходя из этих данных можно рассчитать максимальную линейную скорость движения ленты, которая составит 1200 м/мин. Она ограничивается при помощи частотного преобразователя, подключенного к двигателю.Конструкция.Конструкция станка довольно простая, и при этом очень жесткая за счет своей массивности, так как в ее основу заложен лист толщиной 12 мм. Из него выполнено основание под асинхронный двигатель, к фланцу которого в свою очередь прикручена плита, образующая несущую раму всего станка. Чтобы хоть немного разгрузить фланец электродвигателя, основание и несущая рама связаны друг с другом через деталь - направляющую штанги. Далее в нее вставляется сама штанга, на один из концов которой крепится пластина, несущая на себе деталь в виде «полумесяца», а также направляющую для механизма установки рабочего столика. На концах «полумесяца» имеются два ролика, а через центр проходит ось, позволяющая поворачивать эту сборочную единицу под разными углами. Еще в состав сборочной единицы – «полумесяца», входит направляющий упор для шлифовальной ленты.На несущей раме через ось закреплен рычаг с роликом для центрирования шлифовальной ленты. Этот рычаг так же играет роль натяжителя, в виду того, что между ним и рамой установлен газлифт.Рабочие поверхности ведущего шкива и натяжного ролика имеют полукруглый усеченный профиль для лучшего удержания ленты на их поверхности.Механизм крепления рабочего столика имеет несколько степеней свободы, это делает его позиционирование очень удобным для последующей работы. ![]() Изготовление и сборкаПроектирование этого станка продолжалось довольно долгое время. Все как я люблю – смоделировал в CAD программе, и раскидал деталировку с чертежами. Механической обработки получилось много, ее отдал другу – он занимается металлообработкой. Кроме токарных и фрезерных работ, требовалось изготовить еще ряд деталей из листового железа. Как вы уже, наверное, догадались, эти детали заказал на лазерной резке. В итоге, через некоторое время у меня в мастерской появился увесистый ящик с железом. И тут я смекнул: - «Если толком ничего не заработает, то при нынешних ценах на металл, сдам все в чермет и выйду в нули» (шутка конечно). Некоторые детали дорабатывал сам: сверлил отверстия, нарезал резьбы, сваривал, даже немного фрезеровал на своем СФ – 16 (но это отдельная история, так как опыта и знаний маловато). В общем, всю слесарную работу делал сам. Двигатель был куплен заранее.Началась сборка. Так как все было сделано по чертежам, то в целом собиралось хорошо - кайфанул. Но и без проблемных мест не обошлось, я все же человек, а людям, как известно, свойственно ошибаться. В паре деталях ошибся с размерами, в моделях, конечно, сразу все поправил, а вот с железом пришлось немного потрудиться, но и с ним все решилось.После предварительной сборки и пробного пуска, последовала разборка и покраска. Красить сам не стал, отдал «специалистам», все детали были отпескоструены и разделены на те, которые надо покрасить и на те, которые надо покрыть хим. оксидом. Покрасил уже традиционно в синий глянец, полимерной порошковой краской.Извините, данный ресурс не поддреживается. :( Работа и настройкаТак как у меня имелся частотный преобразователь на 1,5 кВт, то настройка упростилась. Вся настройка сводится к тому, чтобы при раскручивании ленты она не слетала с роликов и находилась всегда в одном и том же положении при прикладывании к ленте обрабатываемой детали.Для того чтобы ленту отцентровать, запустил вращение на малых оборотах и установочным винтом отрегулировал положение натяжного ролика. Далее постепенно увеличивал скорость вращения, чтобы убедиться, что лента отцентрована во всем диапазоне скоростей.Приступил к испытаниям. После прикладывания обрабатываемой детали к ленте, она начала смещаться в сторону. Отрегулировал положение направляющего упора между двумя роликами, расположенными на детали в виде «полумесяца». Ролики и направляющий упор должны находиться в одной плоскости, для этого даже пришлось отфрезеровать упор в угол, так как после сварки его немного повело.На этом основная настройка закончена, и можно приступать к работе. Тут многое зависит от обрабатываемого материала и требуемой шероховатости, которую необходимо получить, а, следовательно, для этого надо подбирать зернистость ленты и скорость ее вращения.Работать на этом станке еще только предстоит учиться, но уже кое-какой опыт получен.Извините, данный ресурс не поддреживается. :( Выводы и рекомендацииВ ходе эксплуатации также обнаружился пока один, но довольно весомый недостаток конструкции: не хватает мощности. Решения два: поставить мотор мощнее или уменьшить диаметр ведущего шкива. Второй вариант пока более предпочтителен, но с диаметром еще не определился.Возможно, в будущем переделаю немного основание для того чтобы была возможность поворачивать рабочую часть в горизонтальное положение. А в остальном пока все устраивает. Вариантов доработки конечно много, это и магнитный столик на каретке для шлифовки плоскости и всевозможные приспособы для удержания заготовок, установка дополнительных роликов и колёс различного диаметра и т.д. Вопрос ценыГриндер получился не из бюджетной категории. Подобного по качеству изготовления из того, что продается в Интернет-магазинах, я не видел. Местами можно конструкцию немного облегчить и тем самым удешевить, но не вижу особого смысла, так как станок изначально делался для себя. То, что продается в основном слеплено из листа заниженной толщины, нарезанного чпу лазером, все рассчитано на низкую себестоимость. Но самое главное то, что все они работоспособные и не важно, сколько металла в них заложено. =========== Источник: habr.com =========== Похожие новости:
DIY или Сделай сам ) |
|
Вы не можете начинать темы
Вы не можете отвечать на сообщения
Вы не можете редактировать свои сообщения
Вы не можете удалять свои сообщения
Вы не можете голосовать в опросах
Вы не можете прикреплять файлы к сообщениям
Вы не можете скачивать файлы
Вы не можете отвечать на сообщения
Вы не можете редактировать свои сообщения
Вы не можете удалять свои сообщения
Вы не можете голосовать в опросах
Вы не можете прикреплять файлы к сообщениям
Вы не можете скачивать файлы
Текущее время: 26-Авг 03:33
Часовой пояс: UTC + 5