[DIY или Сделай сам] Переделка CNC 3018 Pro на рельсы. Личный опыт. Часть 2
Автор
Сообщение
news_bot ®
Стаж: 7 лет 6 месяцев
Сообщений: 27286
Здравствуйте, продолжаю описание доработки оси Y. Первая часть тут.Один из посылов этой части: учитесь читать чертежи/эскизы/картинки, и обращать внимание на мелочи.Вполне допускаю, что некоторые термины, с точки зрения профессиональных токарей/фрезеровщиков/слесарей и т.д. не совсем верны, но повторюсь, я описываю свой личный опыт без какой-либо "проверки" в инете (всё из моих мозгов, так сказать тест :) ) Да и сам то я "любитель" в этом плане.В первой части я сделал:- обрезку профилей (и по X оси тоже) и их торцевание (кстати, лишнее я пилил ручной ножовкой, и затем на станке доводил);- нарезка резьбы в профилях;- сверление отверстий в передней/задней планках;- сборка (и не забудьте в "серединные" профили вложить Т гайки (по 12шт.) для рельс, и по боковым профилям гайки для крепления штатной оси X);По сборке вроде вопросов быть не должно.Всё же опишу один нюанс, который покажется смешным, но мне реально звонили двое коллег из разных контор где я работал, и они спрашивали: "я собираю диван/тумбу и тут две шайбы, одна какая-то кривая и она не цельная, а другая нормальная, и я не знаю, что ставить вначале на болт". Грустно, но в своих областях они "шарят" очень хорошо. Речь конечно о гровер шайбах и обычных.Скажу кратко: гайки и шляпки болтов очень любят гроверы, они прям таки их ищут, и хотят слиться с ними в экстазе, без всяких посредников :) Всё!Пластина, на которую крепятся две каретки (чертеж из исходной статьи).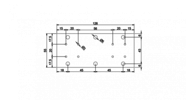
Разберу чертеж поподробнее: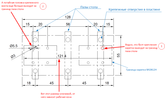
На данной картинке забыл обозначить размеры самой каретки, они 45.4x27.У автора чертежа, размер между краями кареток, равен 121.4мм. - в итоге, ход столика за счет ширины "тандема" кареток составляет 300-121.4= 178.6мм., т.е. ход столика меньше на 1.4мм. (стол 180мм.) Мне лично это не понравилось, и я сдвинул каретки на 1мм., но тут возникает проблема - две пары винтов, крепящие каретки по краям, сдвигаются в пазы стола (они впотай, так что ничего страшного), но они будут в воздухе (а может и нет, как пластина "ляжет" к столику), могут отвернуться винты- тут я ступил.Но в итоге я сверлил по своим размерам:
Получилось чуть меньше 120мм. между каретками, и полный ход столика.Небольшое примечание по поводу ширины планки, а именно, почему она такая ?.Гайки крепления к столику, это имбусы (в принципе можно и другие шляпки использовать, просто, допустим шестигранник не очень удобен, хотя, если есть торцевая головка, то пофигу), диаметр головки всё равно будет примерно 10мм. Получаем: ширина каретки 27мм. + два винта по 10мм. = 47мм.Но это ещё не всё, шайбы нам картину портят.Диаметр гровер шайбы под болт М6 = 11.5мм. Диаметр обычной шайбы = или 12мм. или 13мм. Вот и считаем: 27+13+13 = 53мм. Автор чуть увеличил на всякий, и получается 55мм.Я это к чему.В своём городе, в "обычных" магазинах, я не нашел алюминиевых пластин, размерами больше 50мм. и толщиной 3 и более мм. (заказать то конечно можно под размер). Или, как безысходный вариант, найти алюминиевые уголки 50х50х3 (а они продаются в Леруа, Максидом, Мегастрой и т.д.) и отрезать одну сторону уголка, но максимум мы "выжмем" 47мм. (уголки по внешним размерам указываются). Т.е., по расчетам выше, мы "впритык". Можно и так, но придется отказаться от обычных шайб (гровер сместится при закручивании). Так же нельзя будет использовать обычные шестигранные головки, т.к. размер у них по углам = 11мм. (ну если только разнести отверстия чуть ближе к краям).Итого.Нужно искать пластины размерами 126х55х3. Длина и ширина пластин пофигу, в плане увеличения, т.е. можно 130х60 к примеру (такие я "попросил" у знакомых на заводе). Толщина… ну смотрите, в эту толщину будут вставляться винты, диаметром 3мм. с потайной головкой. Высота головки 1.65мм. для винта М3 длиной 6мм.Глубину зенковки найдете в инете.Тут оговорка… у меня есть винты M3 с потайной головкой длиной 20мм., и эти винты не встают в раззенкованное отверстие глубиной 1.65мм. - нужно зенковать больше - поясните плиз, почему. Я в плане стандартов спрашиваю, понятно, что могу померить, но все же.В итоге, толщина у пластины для винта впотай, "скрашивается" до, грубо говоря, 1мм. - это нормально в том плане, что после зенковки, диаметр "остатка" отверстия не увеличивается. Но, как и пишет автор статьи: "не используйте в качестве зенкера сверло" (у сверла другой угол заточки, не 90град, как у зенкера) . В итоге принимаем толщину 3мм. (мне с завода дали 2.9мм.) Можно толще, но при этом учтите, что пластина должна быть прямой. При толщине пластины 3мм. и зажав её 6ю болтами М6, она сама станет прямой ИМХО.На заметку.При заказе винтов с потайной головкой, имейте в виду, что высота самой головки входит в длину винта.Почему я оперирую длиной рельс 300мм., если у меня длина профилей 290мм. ?Отвечаю.Рельсы расположены на профилях, верхняя грань которых совпадает с планками. Поэтому я не стал резать рельс 300мм. и прикрепил его с вылетами на планки. Нюанс: профили могут быть чуток ниже планок (ошибка с разметкой - бывает), главное, чтобы ошибка была по двум сторонам планок одинаковая. У меня такого не было, но всё же я сделал пазы в планках, чтобы быть уверенным, что рельсы кладутся на профили, а не на планки.Пазы (глубина 1мм., ширина 14мм., т.е. заведомо шире, чем ширина профиля, т.к. профиль при юстировке может чуток уйти вбок):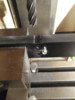
Если нет станка, то это очень легко сделать надфилем (руками я такие операции делал), планки легко растачиваются. С планками закончили.Сверловка пластин. Что на станке, что "ручками" - одно и тоже ("ручками" - есть нюансы).Станок.По хорошему, если бы станок был оборудован УЦИ (это первая попавшаяся ссылка, не реклама), то было бы всё проще. У меня УЦИ нет, хотя пишу прошивку для него и уже собрал тестовую плату. Прошивка универсальная (в определенных пределах конечно), чтобы поддержать как можно больше "линеек". Теперь не реклама: ссылка на статью про мою реализацию тут . Пока времени на прошивку нет, (хотя уже добавил много чего в неё, но на гит не выкладывал), поэтому приходится довольствоваться тем что есть, а именно, лимбами.На станке по осям X/Y конечно есть люфт, и вот из-за этого люфта я не стал отмерять всe отверстия по лимбам станка, т.к. ошибешься, и всё по новой.Сверловку я делал по наклейке, которую распечатал на струйнике (использовал самоклейку). И опять таки сверил две пластины вместе (если пластины не одинаковые по ширине, то их нужно отторцевать, чтобы в тиски зажались обе). Или же, сверлить их по отдельности и на каждой - наклейка.
Совет.Между губками тисков и заготовкой (а в нашем случае двух заготовок друг на друге), подложите полоски обычной газеты - толщины газетной полоски хватит, чтобы хорошо зажать заготовку (газетка действует как... ну пусть будет "демпфер" между губкой тисков и заготовкой). Газетку можно чуток смочить маслом, чтобы она прилипла к губкам.Наклейку я конечно наклеил неровно, относительно граней пластины. И вы наклеите её неровно, даже, если наклейка будет в размер пластины - это факт (обрезка наклейки, совмещение). Это не мешает, т.к. нужно относительное расстояние между отверстиями.Теперь самый гемор:- нужно совместить центр каждого отверстия с центровочным сверлом;- сделать предварительную сверловку;- просверлить "обычным" сверлом;И такая последовательность для каждого отверстия :(Почему вначале центровочное сверло: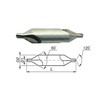
"Обычное" сверло относительно длинное, и оно может "уехать" от точки сверления - биение сверла, жесткость. А после центровочного сверла, "обычное" войдет в отверстие сделанное центровочным, по любому. Даже, если сместить центр на станке (ну тогда или сверлу облом или отверстию).Для позиционирования сверла, нужен центроискатель. У меня такой:Извините, данный ресурс не поддреживается. :( К этому видео, ремарка.При работе со станками, никогда не пользуйтесь перчатками/рукавицами - только голые руки и без всяких обручальных колец и т.д.! По поводу обручального кольца, можете поискать в инете (у чувака всю кожу с пальца кольцо сняло, вплоть до костяшек). Так же, длинные волосы, в шапку! Это не шутка :(. Последствия найдете в инете.Продолжу по центроискателю.Он хорош, но вылет у него уж очень большой вместе с его патроном, и в плане "поднимать/опускать стол станка" (конструктив у моего станка такой), не очень удобно. В итоге плюнул и стал использовать твердосплавное сверло для ПП 0.3мм. (оно короче). Нахождение центра :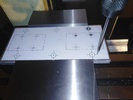
И дальше, для каждого отверстия, подводим сверло (а-ля "центр") на минимальной высоте и совмещаем с "крестом" центра на бумажке (очки, лупа и т.д., от зрения зависит). И сверлим по шагам (центровка, смена сверла), как описал выше.Сверловка руками.Алюминий относительно мягкий металл по сравнению со сверлом, которое хочет его просверлить, и с обычным кернером. Поэтому, разметку будущих отверстий в алюминии я делаю при помощи иглы для ручного шитья (самой толстой). Можно делать разметку очень тонким шилом (у меня такого не было, поэтому игла). Выставляем иглу на крест бумажки (опять таки очки, лупа) и тихонечко постукивая молотком по игле, делаем лунку в заготовке.По бумажке лучше таким образом разметить все отверстия, и затем бумажку удалить.Затем, очень нежно (без нажима, только вес самого инструмента), шуруповертом/дрелью со сверлом порядка 1-1.5мм. делаем лунку в разметке. Очень желательно делать это под 90град., т.к. любой наклон сверла уведет размеченную лунку в сторону (проходил это). Т.е. процесс ручного сверления алюминия очень тонкий, даже, когда сверлим по кондуктору - имейте это в виду. Вначале лучше просверлить отверстия как можно малого диаметра - порядка 1-1.5мм., и затем нужным диаметром. Тут затык в том плане, что нужно просверлить две пластины (писал выше). Пластины между собой "скрепляем" двухсторонним скотчем (не "уедут" они относительно друг друга, даже, если они изогнуты), и затем кладем их допустим на ЛДСП, и потом крепим струбцинами к столу, примерно так (ЛДСП забыл подложить, но фото один фиг постановочное): 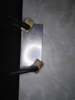
Далее.Или сверлим четыре отверстия по краям, и одно технологическое около центра, и затем по этим отверстиям скрепляем две пластины вместе (если не верим скотчу). И потом сверлим остальные.Или сразу сверлим все отверстия без промежуточного крепежа.Затем рассверливаем все отверстия, уже по кондуктору, вначале сверлом 3мм., а отверстия, где нужен диаметр 6мм., я бы рассверливал вначале "промежуточным" сверлом 4.5мм., затем 6мм. (и отверстия 3мм. я бы тоже вначале рассверлил промежуточным сверлом).После сверления, у отверстий остаются кромки. Чтобы их убрать, я их "зенкую": отверстия 3мм. сверлом 6.5мм., отверстия 6мм. сверлом 10мм. (это мои подборки диаметров сверл для "зенковки"), ручками - это легко.Пластины просверлены, нужно сделать зенковку под потайные винты крепежа кареток.На станке.Что на станке, что руками, я сделаю это при помощи зенкера, который у меня был в наличии, вот такого:
Он по дереву, но пишут, что может работать по цветмету (очень плохо он работает по алюмишке, т.к. режущих кромок много). Для алюминия, думаю, достаточно двух режущих кромок (поправьте, если не так).Почему плохо работает? Стружка забивается между режущих кромок и приходилось вычищать стружку кистью.Ну что есть, то есть.Станок.Чтобы сделать зенковку, вначале зенкер нужно отцентровать по каждому отверстию. По хорошему это делается при помощи того же индикатора ИРЦ (диаметр шарика у него примерно 2мм.) а отверстия под зенковку у нас 3мм., или при помощи более "взрослых" приспособлений, например такое (видео взял первое попавшееся, см. с 8:37):Извините, данный ресурс не поддреживается. :( Просто при помощи ИРЦ не очень удобно находить центр, т.к. сам индикатор крутится - о вращении при помощи движка станка можно забыть и вращать шпиндель только руками. Короче голова кругом пойдет :)Я поступил "дедовским" методом.Зажимаю пластину в тиски.В патрон зажимаю сверло 3мм. наоборот, чтобы на выходе был хвостовик сверла. Зажимаю в легкую, так, чтобы сверло не выпало из патрона, но в то же время сместить вверх или вниз руками, было трудно. Далее, подвожу пластину к отверстию, и стараюсь сделать так, чтобы сверло, при перемещении пластины вверх, вошло в отверстие (бывает не видно нифига, входит сверло или нет - делаю метку маркером на хвостовике сверла). Как то так:Промахнулись (утрирую конечно):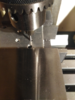
Попали: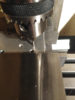
И затем поднимаю стол, и, если сверло не уходит вверх, а "вставляется" в отверстие, считаем что центр найден.Зенковка.Станок.Вот честно, не знаю, как найти по простому поверхность, относительно которой нужно зенковать (будут советы, типа: "считай и т.д." - неохота :) ) Но это в данном случае. Я делал так: включил станок, подвожу зенкер к заготовке, и как услышу писк, то считаю, что от этого уровня нужно углубляться на... 1.65мм. Если есть другие варианты в данном случае, то попрошу описать, заранее спасибо!Таким образом зенкуем 8 отверстий в каждой пластине (у нас их две). Гемор ещё тот.Руками.Зенкер в шуруповерт/дрель и вручную, потихоньку проходимся по каждому отверстию (именно по алюмишке не пробовал, но по ЛДСП - без проблем).Получилось так: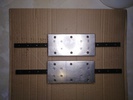
Осталось изготовить центральную пластину для крепления гайки.Вот тут, опять таки извиняюсь, кто живет в "глубинке". В Казани я нашел пластину 40х3 длиной 1м. И по чертежу (да да, не по ГОСТу чертеж) изготовил такую пластину: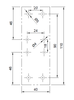
Распечатал наклейку, и наклеил её на заготовку. И далее просверлил отверстия (что станок, что ручками - всё выше описано). Опять таки, центровка наклейки нам не важна, нам нужны относительные размеры. Если нужно, скину чертеж в pdf.С одного края пластины нужно сделать проточки, т.к. пластина будет упираться в винты крепления шаговика.Далее, нужно сделать опоры между пластиной и столиком.Я их делал из обрезков профиля, которые остались после отрезки профилей для оси X (отверстия как раз для крепления профиля 2040). Вот не скажу я вам нужную высоту профилей, делал по месту. Получилось так: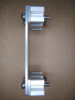
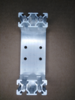
Видите проставки между пластиной и профилем... Это я с размером ступил. Пришлось вот так поступить. Хотя есть варианты, навскидку:- есть алюминиевые квадратные прутки 16мм. + нужно порядка 2мм. и более на проставку;- тупо болты с гайками;Реальную высоту я не пишу, т.к. тут по месту нужно подбирать.И с одного края пластины вырезы для винтов, которые крепят шаговик (да, надфилем, и получилось колхозно):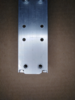
В итоге получилось так: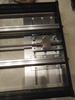
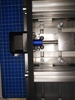
Позволю себе выложить два видео, где видно/слышно как люфтит гайка в крайних положениях. А это значит, что высота центральной пластины отъюстирована, и это отлично!Извините, данный ресурс не поддреживается. :( Извините, данный ресурс не поддреживается. :( Осталось отъюстировать сам столик, а это уже отдельная статья (кучеряво юстировать....). И про гайку нужно подумать.Всем спасибо!
===========
Источник:
habr.com
===========
Похожие новости:
- [Разработка робототехники, Разработка под Arduino, Умный дом, DIY или Сделай сам, Электроника для начинающих] Cамодельная автоматика пеллетной горелки на базе Arduino nano
- [Беспроводные технологии, DIY или Сделай сам, Электроника для начинающих] Победа над nRF24L01: на три шага ближе
- [DIY или Сделай сам, Электроника для начинающих] Универсальные платы для умного дома на базе микроконтроллера ATmega128 (ATmega2561)
- [Big Data, Промышленное программирование, Разработка для интернета вещей] Вебинар «Удаленный мониторинг станков. Рассказываем, показываем, подключаем»
- [Ненормальное программирование, Разработка под Arduino, DIY или Сделай сам, Электроника для начинающих] Измеритель расстояния на HC-SR04 без микроконтроллера
- [Программирование, Социальные сети и сообщества, DIY или Сделай сам] ClubHouseRec_bot — расцвет и падение или как записать беседу бесплатно и без смс
- [Схемотехника, Производство и разработка электроники, Физика, DIY или Сделай сам, Электроника для начинающих] Эксперименты с карбидом кремния (SiC): замедление переключения SiC-MOSFET
- [Разработка под Arduino, DIY или Сделай сам] Схема моего умного дома на основе ESP8266
- [Open source, Разработка игр, Графический дизайн, Дизайн игр, DIY или Сделай сам] Приглашаю к созданию русской народной игры «Колобок»
- [C++, Разработка под Arduino, DIY или Сделай сам, Data Engineering] ESP 8266: отправка данных на сайт методом Get запроса
Теги для поиска: #_diy_ili_sdelaj_sam (DIY или Сделай сам), #_chpu (чпу), #_cnc, #_cnc3018, #_diy_ili_sdelaj_sam (
DIY или Сделай сам
)
Вы не можете начинать темы
Вы не можете отвечать на сообщения
Вы не можете редактировать свои сообщения
Вы не можете удалять свои сообщения
Вы не можете голосовать в опросах
Вы не можете прикреплять файлы к сообщениям
Вы не можете скачивать файлы
Текущее время: 26-Авг 13:15
Часовой пояс: UTC + 5
Автор | Сообщение |
---|---|
news_bot ®
Стаж: 7 лет 6 месяцев |
|
Здравствуйте, продолжаю описание доработки оси Y. Первая часть тут.Один из посылов этой части: учитесь читать чертежи/эскизы/картинки, и обращать внимание на мелочи.Вполне допускаю, что некоторые термины, с точки зрения профессиональных токарей/фрезеровщиков/слесарей и т.д. не совсем верны, но повторюсь, я описываю свой личный опыт без какой-либо "проверки" в инете (всё из моих мозгов, так сказать тест :) ) Да и сам то я "любитель" в этом плане.В первой части я сделал:- обрезку профилей (и по X оси тоже) и их торцевание (кстати, лишнее я пилил ручной ножовкой, и затем на станке доводил);- нарезка резьбы в профилях;- сверление отверстий в передней/задней планках;- сборка (и не забудьте в "серединные" профили вложить Т гайки (по 12шт.) для рельс, и по боковым профилям гайки для крепления штатной оси X);По сборке вроде вопросов быть не должно.Всё же опишу один нюанс, который покажется смешным, но мне реально звонили двое коллег из разных контор где я работал, и они спрашивали: "я собираю диван/тумбу и тут две шайбы, одна какая-то кривая и она не цельная, а другая нормальная, и я не знаю, что ставить вначале на болт". Грустно, но в своих областях они "шарят" очень хорошо. Речь конечно о гровер шайбах и обычных.Скажу кратко: гайки и шляпки болтов очень любят гроверы, они прям таки их ищут, и хотят слиться с ними в экстазе, без всяких посредников :) Всё!Пластина, на которую крепятся две каретки (чертеж из исходной статьи). ![]() Разберу чертеж поподробнее: ![]() На данной картинке забыл обозначить размеры самой каретки, они 45.4x27.У автора чертежа, размер между краями кареток, равен 121.4мм. - в итоге, ход столика за счет ширины "тандема" кареток составляет 300-121.4= 178.6мм., т.е. ход столика меньше на 1.4мм. (стол 180мм.) Мне лично это не понравилось, и я сдвинул каретки на 1мм., но тут возникает проблема - две пары винтов, крепящие каретки по краям, сдвигаются в пазы стола (они впотай, так что ничего страшного), но они будут в воздухе (а может и нет, как пластина "ляжет" к столику), могут отвернуться винты- тут я ступил.Но в итоге я сверлил по своим размерам: ![]() Получилось чуть меньше 120мм. между каретками, и полный ход столика.Небольшое примечание по поводу ширины планки, а именно, почему она такая ?.Гайки крепления к столику, это имбусы (в принципе можно и другие шляпки использовать, просто, допустим шестигранник не очень удобен, хотя, если есть торцевая головка, то пофигу), диаметр головки всё равно будет примерно 10мм. Получаем: ширина каретки 27мм. + два винта по 10мм. = 47мм.Но это ещё не всё, шайбы нам картину портят.Диаметр гровер шайбы под болт М6 = 11.5мм. Диаметр обычной шайбы = или 12мм. или 13мм. Вот и считаем: 27+13+13 = 53мм. Автор чуть увеличил на всякий, и получается 55мм.Я это к чему.В своём городе, в "обычных" магазинах, я не нашел алюминиевых пластин, размерами больше 50мм. и толщиной 3 и более мм. (заказать то конечно можно под размер). Или, как безысходный вариант, найти алюминиевые уголки 50х50х3 (а они продаются в Леруа, Максидом, Мегастрой и т.д.) и отрезать одну сторону уголка, но максимум мы "выжмем" 47мм. (уголки по внешним размерам указываются). Т.е., по расчетам выше, мы "впритык". Можно и так, но придется отказаться от обычных шайб (гровер сместится при закручивании). Так же нельзя будет использовать обычные шестигранные головки, т.к. размер у них по углам = 11мм. (ну если только разнести отверстия чуть ближе к краям).Итого.Нужно искать пластины размерами 126х55х3. Длина и ширина пластин пофигу, в плане увеличения, т.е. можно 130х60 к примеру (такие я "попросил" у знакомых на заводе). Толщина… ну смотрите, в эту толщину будут вставляться винты, диаметром 3мм. с потайной головкой. Высота головки 1.65мм. для винта М3 длиной 6мм.Глубину зенковки найдете в инете.Тут оговорка… у меня есть винты M3 с потайной головкой длиной 20мм., и эти винты не встают в раззенкованное отверстие глубиной 1.65мм. - нужно зенковать больше - поясните плиз, почему. Я в плане стандартов спрашиваю, понятно, что могу померить, но все же.В итоге, толщина у пластины для винта впотай, "скрашивается" до, грубо говоря, 1мм. - это нормально в том плане, что после зенковки, диаметр "остатка" отверстия не увеличивается. Но, как и пишет автор статьи: "не используйте в качестве зенкера сверло" (у сверла другой угол заточки, не 90град, как у зенкера) . В итоге принимаем толщину 3мм. (мне с завода дали 2.9мм.) Можно толще, но при этом учтите, что пластина должна быть прямой. При толщине пластины 3мм. и зажав её 6ю болтами М6, она сама станет прямой ИМХО.На заметку.При заказе винтов с потайной головкой, имейте в виду, что высота самой головки входит в длину винта.Почему я оперирую длиной рельс 300мм., если у меня длина профилей 290мм. ?Отвечаю.Рельсы расположены на профилях, верхняя грань которых совпадает с планками. Поэтому я не стал резать рельс 300мм. и прикрепил его с вылетами на планки. Нюанс: профили могут быть чуток ниже планок (ошибка с разметкой - бывает), главное, чтобы ошибка была по двум сторонам планок одинаковая. У меня такого не было, но всё же я сделал пазы в планках, чтобы быть уверенным, что рельсы кладутся на профили, а не на планки.Пазы (глубина 1мм., ширина 14мм., т.е. заведомо шире, чем ширина профиля, т.к. профиль при юстировке может чуток уйти вбок): ![]() Если нет станка, то это очень легко сделать надфилем (руками я такие операции делал), планки легко растачиваются. С планками закончили.Сверловка пластин. Что на станке, что "ручками" - одно и тоже ("ручками" - есть нюансы).Станок.По хорошему, если бы станок был оборудован УЦИ (это первая попавшаяся ссылка, не реклама), то было бы всё проще. У меня УЦИ нет, хотя пишу прошивку для него и уже собрал тестовую плату. Прошивка универсальная (в определенных пределах конечно), чтобы поддержать как можно больше "линеек". Теперь не реклама: ссылка на статью про мою реализацию тут . Пока времени на прошивку нет, (хотя уже добавил много чего в неё, но на гит не выкладывал), поэтому приходится довольствоваться тем что есть, а именно, лимбами.На станке по осям X/Y конечно есть люфт, и вот из-за этого люфта я не стал отмерять всe отверстия по лимбам станка, т.к. ошибешься, и всё по новой.Сверловку я делал по наклейке, которую распечатал на струйнике (использовал самоклейку). И опять таки сверил две пластины вместе (если пластины не одинаковые по ширине, то их нужно отторцевать, чтобы в тиски зажались обе). Или же, сверлить их по отдельности и на каждой - наклейка. ![]() Совет.Между губками тисков и заготовкой (а в нашем случае двух заготовок друг на друге), подложите полоски обычной газеты - толщины газетной полоски хватит, чтобы хорошо зажать заготовку (газетка действует как... ну пусть будет "демпфер" между губкой тисков и заготовкой). Газетку можно чуток смочить маслом, чтобы она прилипла к губкам.Наклейку я конечно наклеил неровно, относительно граней пластины. И вы наклеите её неровно, даже, если наклейка будет в размер пластины - это факт (обрезка наклейки, совмещение). Это не мешает, т.к. нужно относительное расстояние между отверстиями.Теперь самый гемор:- нужно совместить центр каждого отверстия с центровочным сверлом;- сделать предварительную сверловку;- просверлить "обычным" сверлом;И такая последовательность для каждого отверстия :(Почему вначале центровочное сверло: ![]() "Обычное" сверло относительно длинное, и оно может "уехать" от точки сверления - биение сверла, жесткость. А после центровочного сверла, "обычное" войдет в отверстие сделанное центровочным, по любому. Даже, если сместить центр на станке (ну тогда или сверлу облом или отверстию).Для позиционирования сверла, нужен центроискатель. У меня такой:Извините, данный ресурс не поддреживается. :( К этому видео, ремарка.При работе со станками, никогда не пользуйтесь перчатками/рукавицами - только голые руки и без всяких обручальных колец и т.д.! По поводу обручального кольца, можете поискать в инете (у чувака всю кожу с пальца кольцо сняло, вплоть до костяшек). Так же, длинные волосы, в шапку! Это не шутка :(. Последствия найдете в инете.Продолжу по центроискателю.Он хорош, но вылет у него уж очень большой вместе с его патроном, и в плане "поднимать/опускать стол станка" (конструктив у моего станка такой), не очень удобно. В итоге плюнул и стал использовать твердосплавное сверло для ПП 0.3мм. (оно короче). Нахождение центра : ![]() И дальше, для каждого отверстия, подводим сверло (а-ля "центр") на минимальной высоте и совмещаем с "крестом" центра на бумажке (очки, лупа и т.д., от зрения зависит). И сверлим по шагам (центровка, смена сверла), как описал выше.Сверловка руками.Алюминий относительно мягкий металл по сравнению со сверлом, которое хочет его просверлить, и с обычным кернером. Поэтому, разметку будущих отверстий в алюминии я делаю при помощи иглы для ручного шитья (самой толстой). Можно делать разметку очень тонким шилом (у меня такого не было, поэтому игла). Выставляем иглу на крест бумажки (опять таки очки, лупа) и тихонечко постукивая молотком по игле, делаем лунку в заготовке.По бумажке лучше таким образом разметить все отверстия, и затем бумажку удалить.Затем, очень нежно (без нажима, только вес самого инструмента), шуруповертом/дрелью со сверлом порядка 1-1.5мм. делаем лунку в разметке. Очень желательно делать это под 90град., т.к. любой наклон сверла уведет размеченную лунку в сторону (проходил это). Т.е. процесс ручного сверления алюминия очень тонкий, даже, когда сверлим по кондуктору - имейте это в виду. Вначале лучше просверлить отверстия как можно малого диаметра - порядка 1-1.5мм., и затем нужным диаметром. Тут затык в том плане, что нужно просверлить две пластины (писал выше). Пластины между собой "скрепляем" двухсторонним скотчем (не "уедут" они относительно друг друга, даже, если они изогнуты), и затем кладем их допустим на ЛДСП, и потом крепим струбцинами к столу, примерно так (ЛДСП забыл подложить, но фото один фиг постановочное): ![]() Далее.Или сверлим четыре отверстия по краям, и одно технологическое около центра, и затем по этим отверстиям скрепляем две пластины вместе (если не верим скотчу). И потом сверлим остальные.Или сразу сверлим все отверстия без промежуточного крепежа.Затем рассверливаем все отверстия, уже по кондуктору, вначале сверлом 3мм., а отверстия, где нужен диаметр 6мм., я бы рассверливал вначале "промежуточным" сверлом 4.5мм., затем 6мм. (и отверстия 3мм. я бы тоже вначале рассверлил промежуточным сверлом).После сверления, у отверстий остаются кромки. Чтобы их убрать, я их "зенкую": отверстия 3мм. сверлом 6.5мм., отверстия 6мм. сверлом 10мм. (это мои подборки диаметров сверл для "зенковки"), ручками - это легко.Пластины просверлены, нужно сделать зенковку под потайные винты крепежа кареток.На станке.Что на станке, что руками, я сделаю это при помощи зенкера, который у меня был в наличии, вот такого: ![]() Он по дереву, но пишут, что может работать по цветмету (очень плохо он работает по алюмишке, т.к. режущих кромок много). Для алюминия, думаю, достаточно двух режущих кромок (поправьте, если не так).Почему плохо работает? Стружка забивается между режущих кромок и приходилось вычищать стружку кистью.Ну что есть, то есть.Станок.Чтобы сделать зенковку, вначале зенкер нужно отцентровать по каждому отверстию. По хорошему это делается при помощи того же индикатора ИРЦ (диаметр шарика у него примерно 2мм.) а отверстия под зенковку у нас 3мм., или при помощи более "взрослых" приспособлений, например такое (видео взял первое попавшееся, см. с 8:37):Извините, данный ресурс не поддреживается. :( Просто при помощи ИРЦ не очень удобно находить центр, т.к. сам индикатор крутится - о вращении при помощи движка станка можно забыть и вращать шпиндель только руками. Короче голова кругом пойдет :)Я поступил "дедовским" методом.Зажимаю пластину в тиски.В патрон зажимаю сверло 3мм. наоборот, чтобы на выходе был хвостовик сверла. Зажимаю в легкую, так, чтобы сверло не выпало из патрона, но в то же время сместить вверх или вниз руками, было трудно. Далее, подвожу пластину к отверстию, и стараюсь сделать так, чтобы сверло, при перемещении пластины вверх, вошло в отверстие (бывает не видно нифига, входит сверло или нет - делаю метку маркером на хвостовике сверла). Как то так:Промахнулись (утрирую конечно): ![]() Попали: ![]() И затем поднимаю стол, и, если сверло не уходит вверх, а "вставляется" в отверстие, считаем что центр найден.Зенковка.Станок.Вот честно, не знаю, как найти по простому поверхность, относительно которой нужно зенковать (будут советы, типа: "считай и т.д." - неохота :) ) Но это в данном случае. Я делал так: включил станок, подвожу зенкер к заготовке, и как услышу писк, то считаю, что от этого уровня нужно углубляться на... 1.65мм. Если есть другие варианты в данном случае, то попрошу описать, заранее спасибо!Таким образом зенкуем 8 отверстий в каждой пластине (у нас их две). Гемор ещё тот.Руками.Зенкер в шуруповерт/дрель и вручную, потихоньку проходимся по каждому отверстию (именно по алюмишке не пробовал, но по ЛДСП - без проблем).Получилось так: ![]() Осталось изготовить центральную пластину для крепления гайки.Вот тут, опять таки извиняюсь, кто живет в "глубинке". В Казани я нашел пластину 40х3 длиной 1м. И по чертежу (да да, не по ГОСТу чертеж) изготовил такую пластину: ![]() Распечатал наклейку, и наклеил её на заготовку. И далее просверлил отверстия (что станок, что ручками - всё выше описано). Опять таки, центровка наклейки нам не важна, нам нужны относительные размеры. Если нужно, скину чертеж в pdf.С одного края пластины нужно сделать проточки, т.к. пластина будет упираться в винты крепления шаговика.Далее, нужно сделать опоры между пластиной и столиком.Я их делал из обрезков профиля, которые остались после отрезки профилей для оси X (отверстия как раз для крепления профиля 2040). Вот не скажу я вам нужную высоту профилей, делал по месту. Получилось так: ![]() ![]() Видите проставки между пластиной и профилем... Это я с размером ступил. Пришлось вот так поступить. Хотя есть варианты, навскидку:- есть алюминиевые квадратные прутки 16мм. + нужно порядка 2мм. и более на проставку;- тупо болты с гайками;Реальную высоту я не пишу, т.к. тут по месту нужно подбирать.И с одного края пластины вырезы для винтов, которые крепят шаговик (да, надфилем, и получилось колхозно): ![]() В итоге получилось так: ![]() ![]() Позволю себе выложить два видео, где видно/слышно как люфтит гайка в крайних положениях. А это значит, что высота центральной пластины отъюстирована, и это отлично!Извините, данный ресурс не поддреживается. :( Извините, данный ресурс не поддреживается. :( Осталось отъюстировать сам столик, а это уже отдельная статья (кучеряво юстировать....). И про гайку нужно подумать.Всем спасибо! =========== Источник: habr.com =========== Похожие новости:
DIY или Сделай сам ) |
|
Вы не можете начинать темы
Вы не можете отвечать на сообщения
Вы не можете редактировать свои сообщения
Вы не можете удалять свои сообщения
Вы не можете голосовать в опросах
Вы не можете прикреплять файлы к сообщениям
Вы не можете скачивать файлы
Вы не можете отвечать на сообщения
Вы не можете редактировать свои сообщения
Вы не можете удалять свои сообщения
Вы не можете голосовать в опросах
Вы не можете прикреплять файлы к сообщениям
Вы не можете скачивать файлы
Текущее время: 26-Авг 13:15
Часовой пояс: UTC + 5